Life sciences A to Z - B is for Biologics License Application
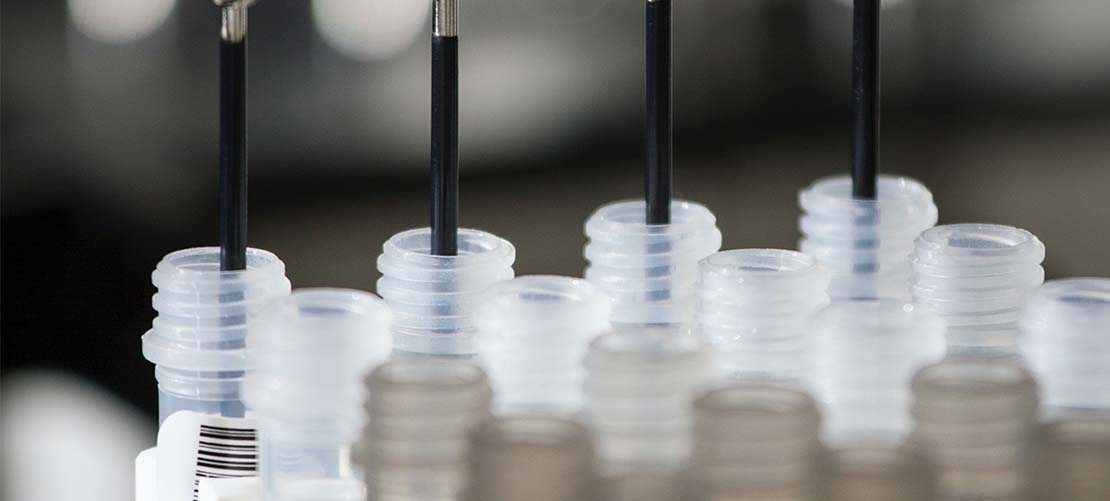
A BLA is a request for permission to introduce, or deliver for introduction, a biologic product into interstate commerce in the US. By way of background, the US has a distinct premarket regulatory pathway for biological products in recognition of their distinct characteristics. Whereas the sponsor of a non-biological drug must submit a new drug application (NDA) showing the drug is safe and effective, a biological product must be licensed pursuant to a BLA showing it is “safe, pure, and potent” as follows:
Safe - “relative freedom from harmful effect”
Pure - “relative freedom from extraneous matter in the finished product”
Potent - “specific ability or capacity of the product, as indicated by appropriate laboratory tests or by adequately controlled clinical data obtained through the administration of the product in the manner intended, to effect a given result”
What is a biologic product?
Biologic products are regulated in the US by the US Food and Drug Administration (FDA) and are used to diagnose, prevent, treat, and cure diseases and medical conditions. Biologic products are a diverse category of products and are generally large, complex molecules. These products may be produced through biotechnology or other cutting-edge methods in a living system, such as a microorganism, plant cell, or animal cell, and are often more difficult to characterize than small molecule drugs. Examples of biologic products include vaccines and other allergenic drug products, blood products and blood components, somatic cells, gene therapy, tissues, and recombinant therapeutic proteins. The nature of biologic products, including the inherent variations that can result from the manufacturing process, can present challenges in characterizing and manufacturing these products that often do not exist in the development of small molecule drugs. It is these characteristics that warrant special treatment when obtaining marketing authorisation.
Given the inherent nature of biologic products, slight differences between manufactured batches (i.e. acceptable within-product variations) are normal and expected within the manufacturing process. Detailed manufacturing information is therefore a critical part of the BLA. As part of the BLA review process, the FDA assesses the manufacturing process and the manufacturer’s strategy to control within-product variations and retain the identity, purity, quality and strength of the drug. These control strategies are put in place to help ensure that manufacturers produce biologic products with consistent clinical performance.
What is the process of BLA submission?
BLA's are submitted to the US Food and Drug Administration (FDA) to request marketing approval of a new biologic medicinal product in the US. Submissions can be made by an legal entity or person involved in the manufacturing of the investigational biologics or an applicant for a license who is ready to take the responsibility for compliance with the establishment and product standards. A BLA must include sufficient material and data for the FDA to determine that the biological product is safe and effective for each proposed indication. A BLA typically includes:
- Data from nonclinical, laboratory, and clinical studies that demonstrate that the biologic meets prescribed requirements of safety, purity, and potency.
- A full description of the methods used to manufacture and package the biologic and the address of each facility involved.
- Samples representative of the product intended to be marketed.
- Samples of the proposed product labelling, enclosures, and containers, including any package insert or prescribing information.
The amount of time that applications spend between initial submission and a final regulatory decision varies. Current FDA performance goals stipulate that FDA intends to review and act on 90% of standard BLA submissions within 12 months of the filing date. The goal for priority review applications is 6 months. As all BLA's are submitted electronically, the first hurdle is to pass an automated technical review. If a submission is missing key components or the study data fail to meet technical conformance criteria, then the application will receive a technical rejection. Assuming the application passes this automated review, the FDA then has 60 days to perform an initial review. During this time FDA will determine if the submission is sufficiently complete to perform a more substantive review. Day 60 post-submission is designated as the filing decision date after which the full review commences.
How can we help?
As mentioned above, information about the manufacturing processes and each manufacturing location must be included in a BLA submission. The FDA may also conduct a Pre-approval Inspection (PAI) whereby a team of experts is sent to the manufacturing facility to assure that the facility is capable of manufacturing the drug and that data submitted with the BLA is accurate and complete. It is therefore essential that manufacturing agreements with the necessary rights are negotiated well in advance of any deadlines for making the BLA submission. We have helped a number of clients put in place the necessary agreements in order to make a BLA submission.